Conventional Electromagnetic Testing
Eddy Current Testing (ET) inspection is based on the interaction between a magnetic field source, a coil, and the electrically conductive material to inspect. This result of this interaction is the induction of Eddy Currents (also known as electromagnetic induction). Discontinuities can then be detected by measuring and analyzing the intensity variations of the current.
Conventional Eddy Current is mainly used to detect surface flaws, to measure conductivity and for gap measurement required by various applications such as the inspection of heat exchangers and aircraft fuselage.
Advantages:
- Excellent surface flaw detection;
- Sensitive to small dimension flaws due to the disturbance in the induced magnetic field;
- No coupling gel or liquid required;
- No surface preparation required.
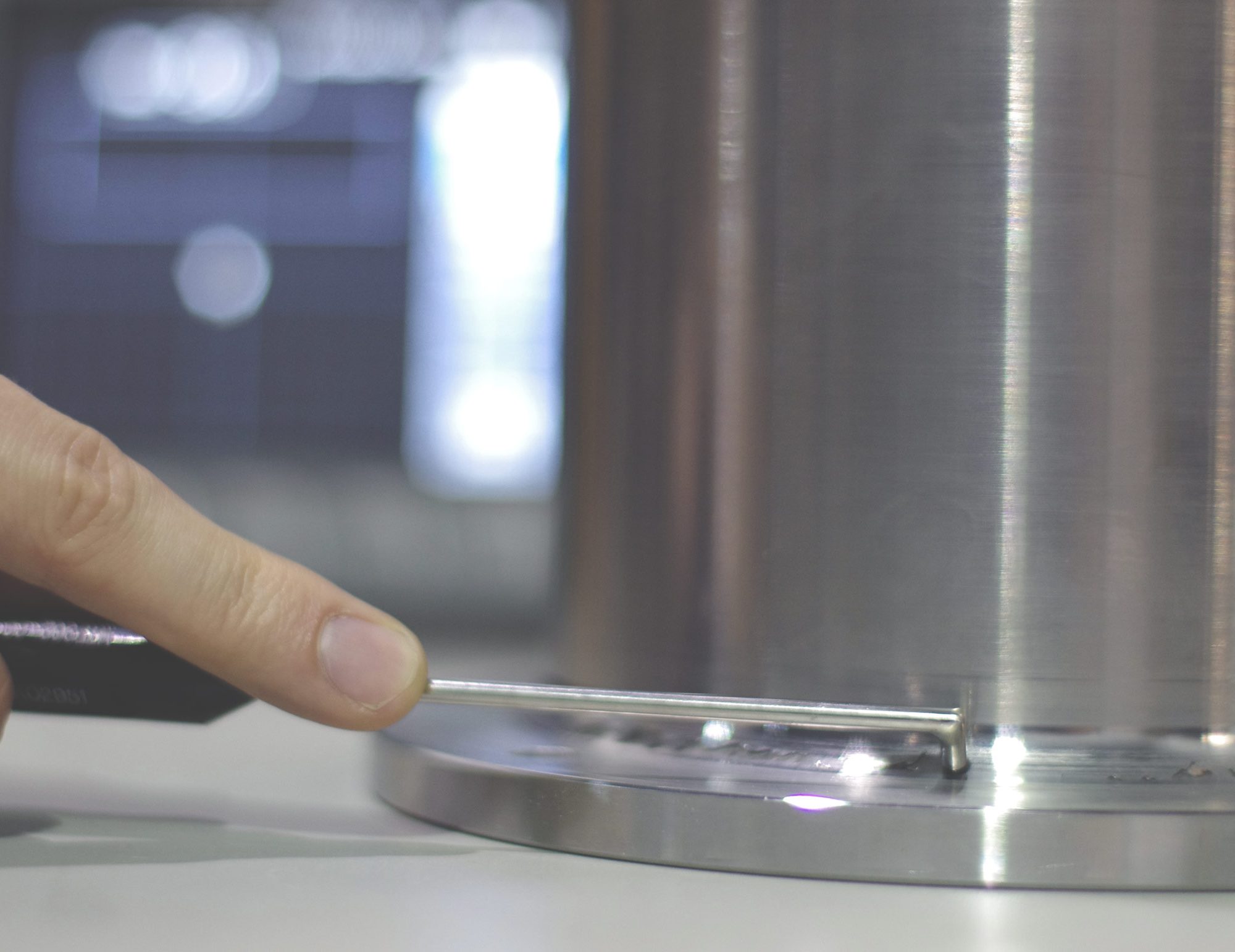
Eddy Current Array (ECA)
Eddy Current Array (ECA) technology represents the evolution of the Conventional Eddy Current method. This technology offers a wider coverage and a greater sensitivity to potential flaws due to the multi-coil design.
Eddy Current Array probes can be customized to best suit the application and required coverage; the number of coils and flexibility of the probe can be adjusted to inspect complex geometries, such as the teeth on gears.
Today, Eddy Current Array is a common method of inspection proving to be effective and cost-efficient in various applications like weld inspection, corrosion mapping, aircraft landing gear, and turbine engine components to name a few.
Advantages:
- More production in less time;
- Data recording;
- Increased probability of detection;
- Suitable replacement of Conventional ECT, MT and/or PT;
- Excellent surface flaw detection;
- Excellent sensitivity to small flaws;
- No coupling or surface preparation required.
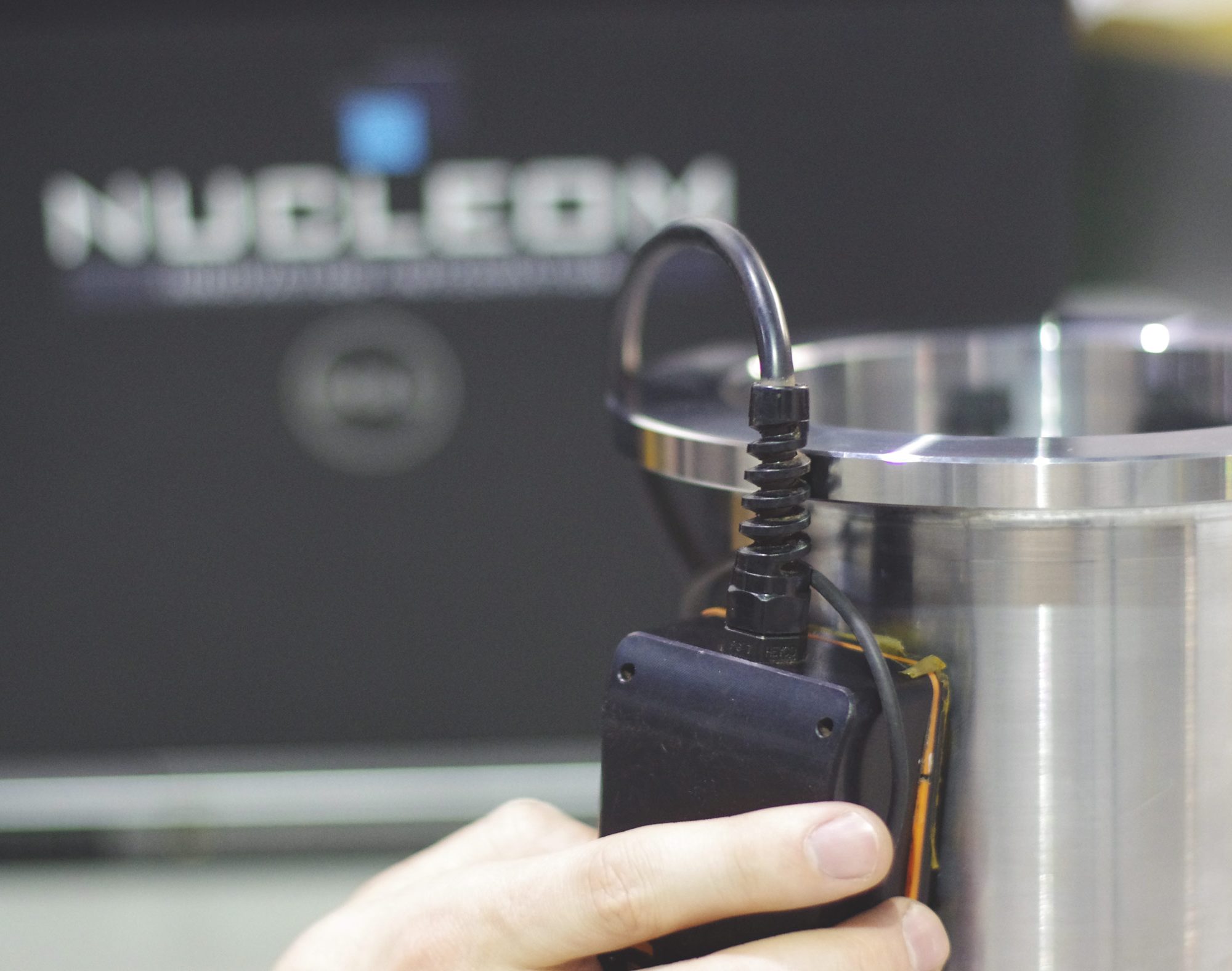
Tangential Eddy Current (TEC)
Tangential Eddy Current (TEC) inspection is another technique based on magnetic induction. The main difference between Tangential and Conventional Eddy Current is that the coils are oriented tangential to the surface. Considering that eddy currents are created perpendicular to the surface, this orientation improves the depth positioning and sizing of flaws.
Tangential Eddy Current is used for the detection and characterization of surface breaking cracks in carbon steel materials. This technology is mainly used on the welds and the heat-affected zone (HAZ). Tangential Eddy Currents can also be regrouped into an Array to increase surface coverage.
Advantages:
- Probe design allows for scanning of the weld cap;
- Detection and characterization of cracks in carbon steel;
- Wider coverage for in a shorter inspection time when using the multi-element Array probe;
- Data Recording;
- Suitable replacement to MT and PT;
- No coupling or surface preparation is required.
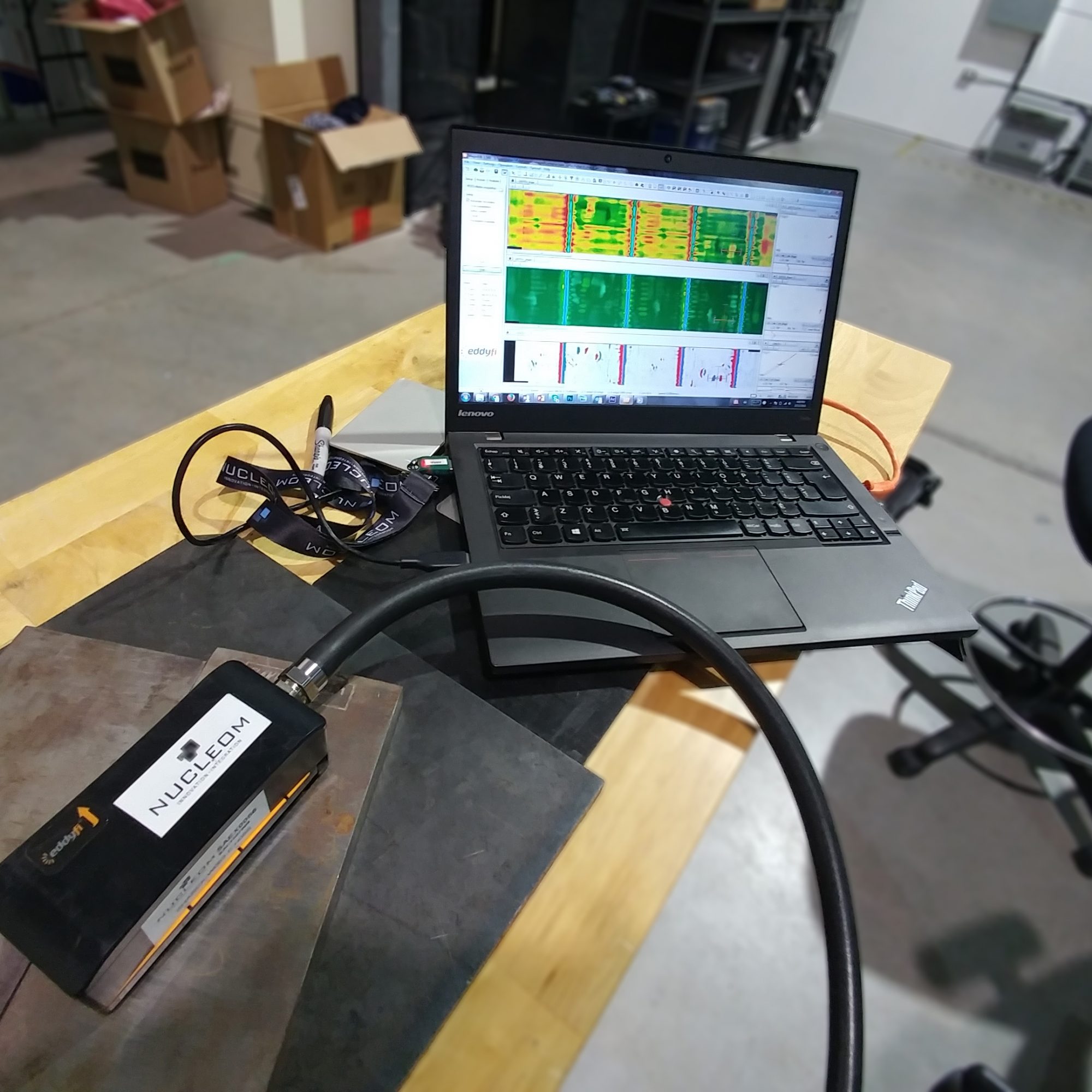
Pulsed Eddy Current (PEC)
Pulsed Eddy Current (PEC) inspection is a technology based on the magnetic field penetration through multiple layers of coating or insulation to reach the surface of a given material and induce eddy currents. This technique is generally used to measure thickness and to detect corrosion on ferrous materials that are covered with an insulation layer, fireproofing, or coating. The main applications are the corrosion detection under insulation (CUI), corrosion under fireproofing (CUF), and corrosion blisters and scabs.
Advantages:
- Inspection through insulation, concrete or other non-conductive material;
- Inspection through aluminum sleeve, stainless or galvanized steel;
- No need to shut down the equipment during inspection;
- No alteration of the insulation material during inspection;
- Probe contact with the component under examination is not mandatory;
- No surface preparation is required;
- Measures the overall thickness of the component.
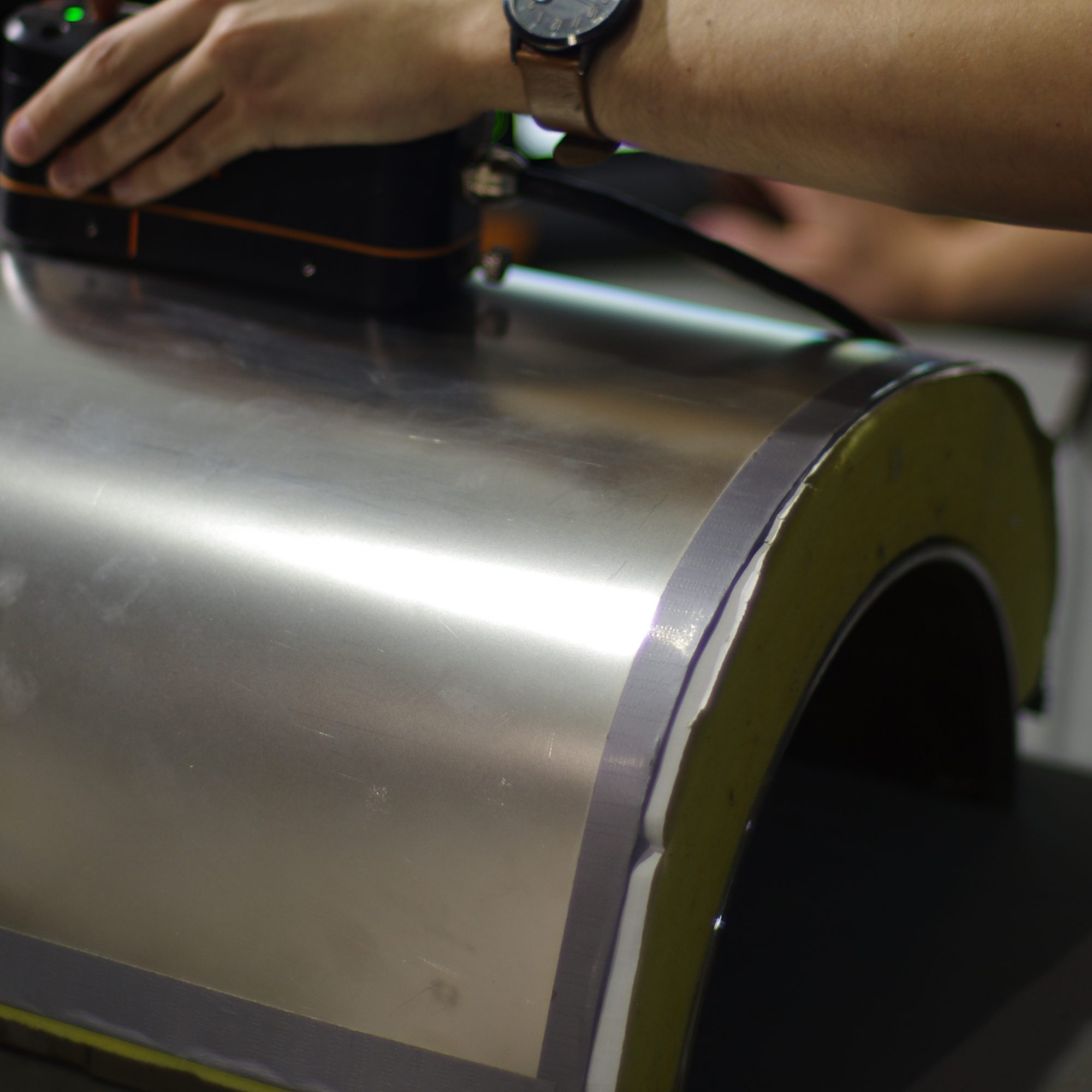
Sucess story : Graphitic corrosion detection in cast iron
One of our clients contacted us to inspect a cast iron pipeline and repair any damage that may have been caused by graphitic corrosion. The challenge was that no conventional screening methods (UT, PAUT, RT) can identify graphitized areas being that no thickness loss or other indication is present. The changes are microstructural, and a non-destructive field method was required to screen the pipeline.
The metallurgy and engineering departments studied the case and put forward the Pulse Eddy Current Array method as the most promising technique to detect graphite areas from the sound section. Graphite and ferrite phases in cast iron does not share the same magnetic properties, hence deferent response to a magnetic field. Tests were conducted in our laboratory and as expected, graphitized zones appeared as thickness wear due to the loss of signal whereas sound area showed a nominal thickness.
We deployed this method for our client to find suitable area for the repair. The inspection provided good results and clearly differentiated the sound cast iron section from the damaged area.
Read more about Graphitic corrosion detection in cast iron
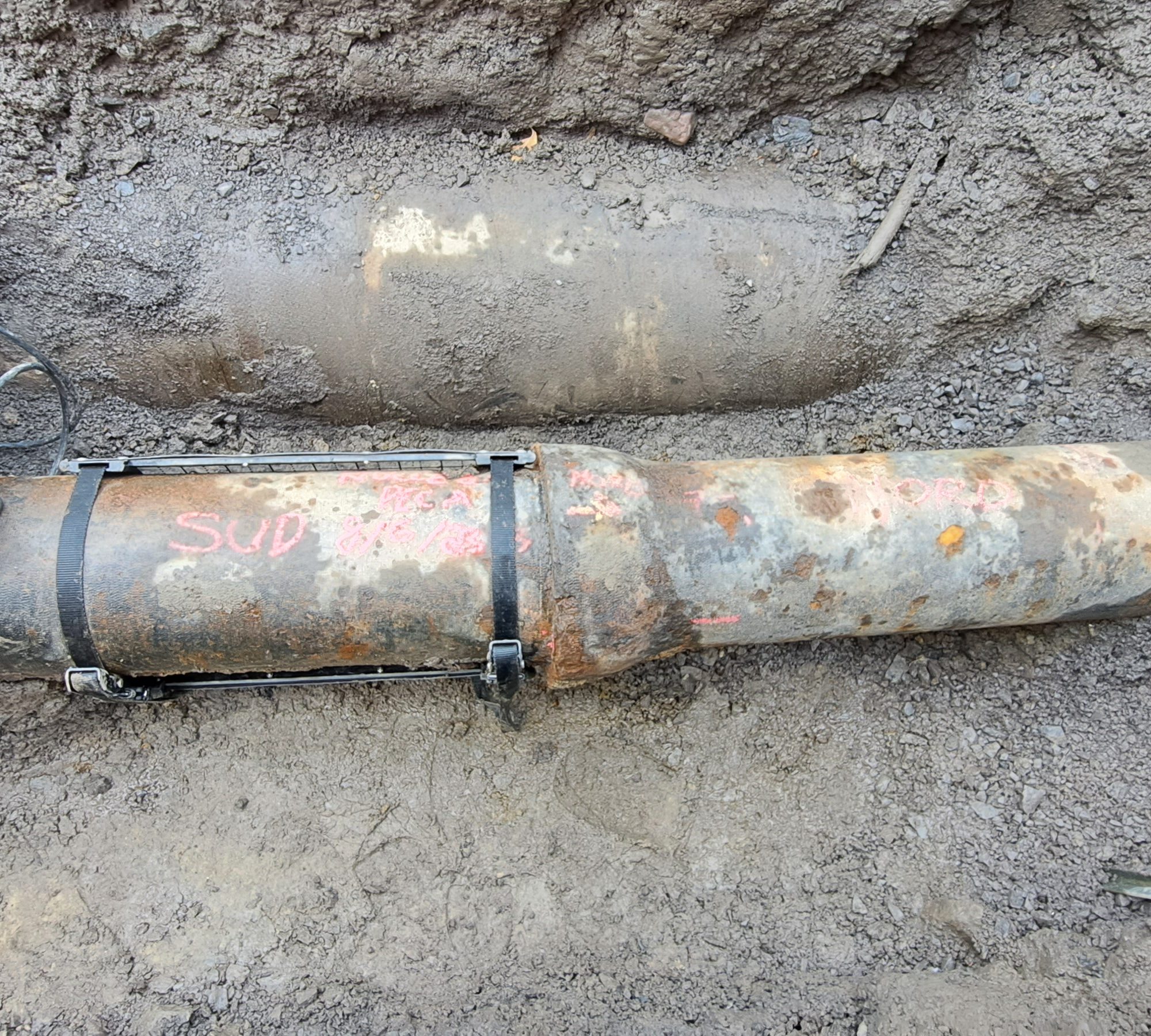
LineCore Technology
The LineCore is an inspection device used to detect internal corrosion in steel-reinforced aluminium conductors (ACSR). The detector is sensitive to the thickness of the zinc coating on the central galvanised steel strands. This zinc layer acts as a sacrificial anode, protecting the cable components. When this layer degrades, internal corrosion occurs and the aluminium strands weaken.
LineCore technology works on the principle of eddy currents. However, the design of the sensor and the analysis display are unique to this inspection technology.
Advantages:
- Quantitative assessment of the remaining protective zinc layer
- Rapid evaluation of a range (speed of 1m/s)
- Enables live and de-energised conductors to be assessed
- Allows evaluation of cables of different diameters (15 to 36.5 mm)
- Three (3) HD cameras for visual assessment of the cable during movement
- Acquisition of encoded data to locate and size the most damaged sections of cable.
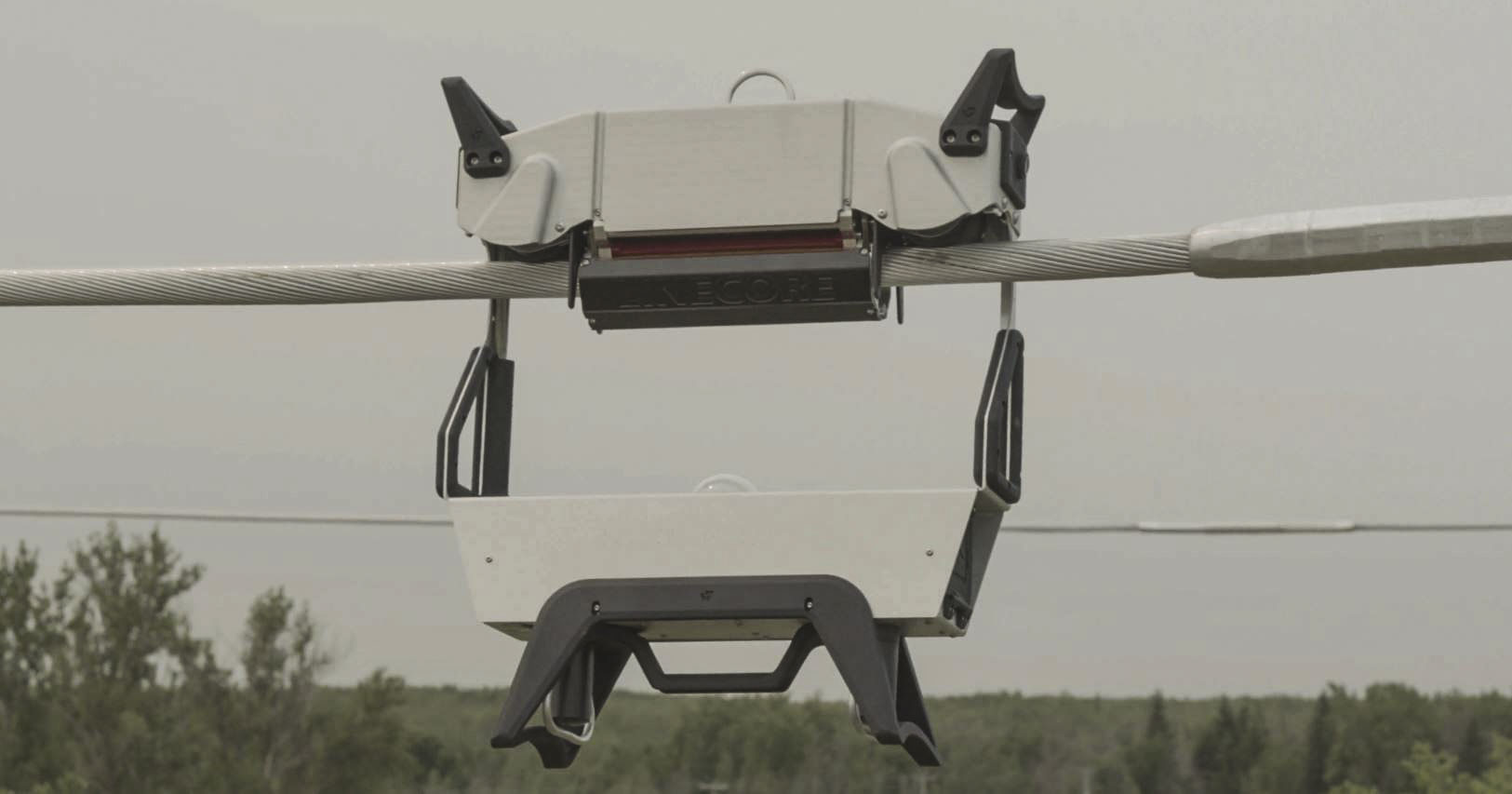
Are you facing inspection challenges?
Our team of specialists is here to assist you. Discover how our services can effectively and professionally address your inspection needs.