Inspection of Urban Water Networks: Detecting Graphitic Corrosion in Cast Iron
In this blog post, we discuss a project carried out for a client who wanted to detect the section to be repaired on one of their cast iron pipelines damaged by graphitic corrosion. Nucleom proposed pulsed Eddy current as the most promising solution for identifying damaged sections of the pipeline from healthy sections. This technique proved to be successful as our team obtained satisfactory results that met our client’s needs.
Introduction to Graphitic Corrosion
Cast iron piping in industry and urban water networks can be subject to graphitic corrosion. This degradation mechanism leads to weakened areas in the pipe that rupture under pressure. The result is product leakage and costly repairs to replace the damaged section. Asset owners want to inspect these pipes to identify damaged sections.
Real-life project
Client issues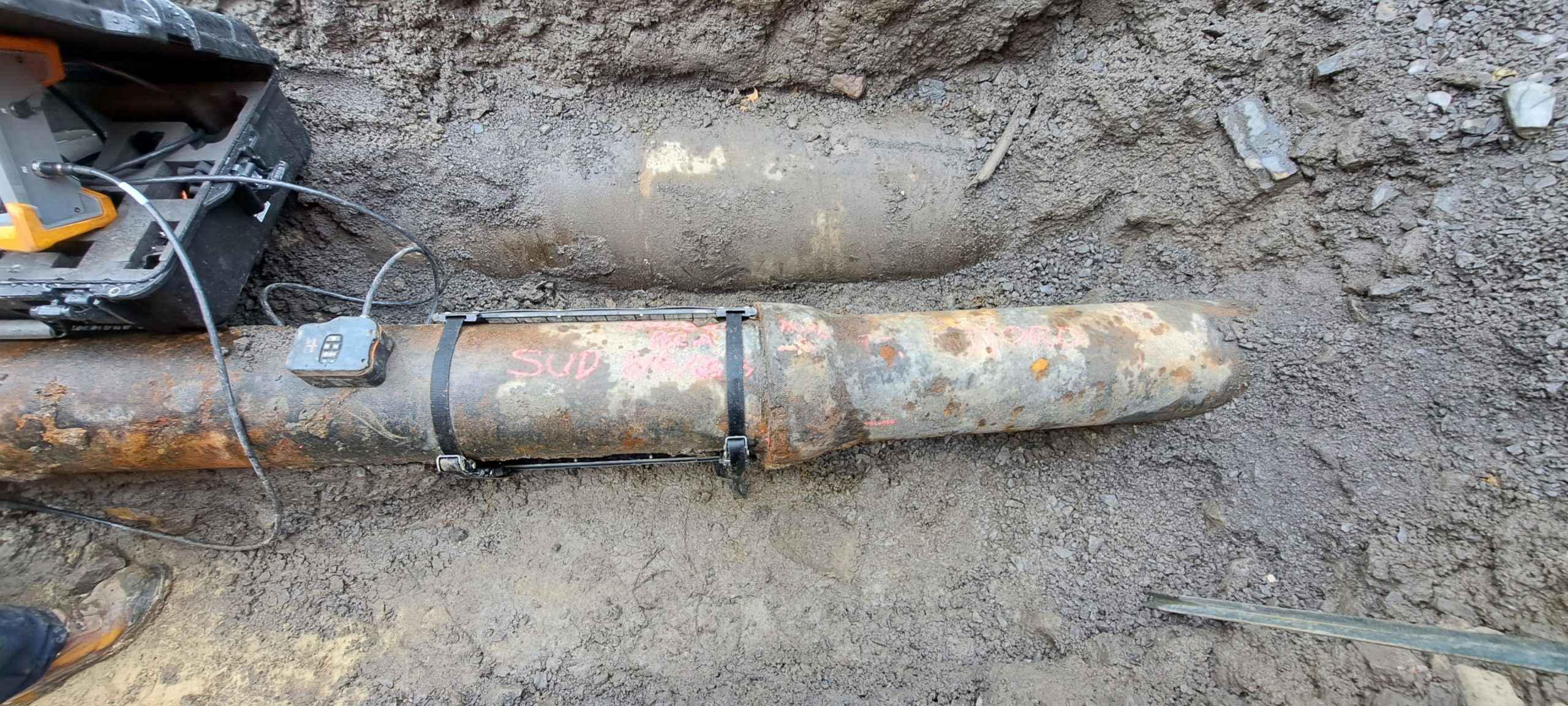
One of our customers contacted us to find sound sections on a cast iron pipeline damaged by graphitic corrosion, in order to repair it. The difficulty was that unconventional inspection method (UT, PAUT, RT) could identify the graphitized area, as there was no loss of thickness or other indication. This was because the changes were microstructural, and a non-destructive method was required to inspect the pipeline.
Solution and benefits for the client
Nucleom’s metallurgy and engineering departments studied the issue and proposed the pulsed Eddy current method as the most promising technique for detecting the graphitized zone from the healthy section: the graphite and ferrite phases in cast iron do not share the same magnetic properties, hence a different response to a magnetic field. Tests were carried out in our laboratory and, as expected, the graphitized zone appeared as a loss of thickness following the loss of signal, whereas the healthy zone has a nominal thickness.
We deployed this method for our client to find the appropriate section for repair. The inspection produced good results, clearly differentiating the healthy section of cast iron (in blue) from the damaged area (in red).
Advantages of Nucleom’s solution
Nucleom’s detection method has made it possible to inspect large surfaces repeatedly over time to monitor corrosion. In addition, we use high-resolution probes that can detect small variations in the magnetic field, enabling the early stages of graphitic corrosion to be identified.
Collaborate with Nucleom
Nucleom combines a range of NDT technologies to increase the reliability of its inspections and the accuracy of its measurements. Working with Nucleom also means having access to complementary solutions such as eddy current, ultrasound, radiology and metallography, in the case of graphite corrosion detection.
If you would like to find out more about our solutions or discuss your inspection requirements, please contact our SALES TEAM. We’re here to help.
For more information on PULSED EDDY CURRENT (PEC)