Destructive Testing and Non-Destructive Testing
The difference between Destructive and Non-destructive testing is the state in which the test piece is found at the end of the inspection process. In some situations, the use of both techniques may be necessary.
What is the difference between Destructive and Non-Destructive Testing ?
As their names suggest, the difference between non-destructive testing and destructive testing is the state in which the test piece is found at the end of the inspection process. With NDT, the item is still intact and undamaged when the testing is completed. With the destructive testing, it is impossible to reuse the component at the end of the process since it is partly destroyed or damaged.
Applications of Destructive Testing
Although there seems to be little benefit in using destructive testing, there are specific situations that require its use:
- Evaluating the mechanical properties of a material, such as the compressive strength, the ductility, the elasticity, the fatigue limit and the resilience;
- Determine service life and detect any design or manufacturing deficiencies that may not appear under usual working conditions;
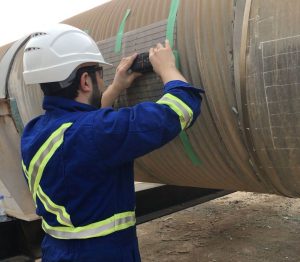
PEC Inspection (Pulsed Eddy Current). NDT allows to keep the insulation and the weather jacket and remove only defective parts.
Those characteristics would be impossible to measure or evaluate simply with non-destructive testing, so this is why destructive testing still has an important place in the industry.
When using NDT versus Destructive Testing ?
Obviously, the size of parts being tested can dictate the type of method that will be most appropriate. Small pieces produced in large quantities (mass production) are more often subject to destructive testing because the cost of destroying some parts is negligible. On the other hand, large structures such as bridges or buildings are very rarely subject to destructive testing because of the high cost of constructing that kind of structure and public safety issues. The use of non-destructive testing is therefore preferred in this type of case.
In some situations, the use of both techniques may be necessary. For example, for the inspection of partial penetration welds, where the goal is to measure the penetration percentage, destructive testing can be used to validate that the results obtained with non-destructive testing are true during technique development or their first implementation. Nucleom has often been involved in such projects, where a validation process for the inspection technique is needed.
If you’re interested in learning more about our NDT SERVICES or would like to discuss your inspection needs, contact our SALES TEAM. We are available to help you in your project.
To learn more about our NDT SOLUTIONS
About Nucleom
Nucleom, a Canadian NDE company founded in the province of Quebec, has been extensively involved in non-destructive examination services in Canada and internationally since 2010. A combination of site experience and NDE tool design know-how gives Nucleom an in-depth perspective of on-site challenges for the NDE system operation. Nucleom’s expertise extends into areas of NDE tool development, tool integration and site inspection campaign execution. Nucleom now has offices in Quebec (Quebec City/Montreal), Ontario (Whitby/Kincardine) and Alberta (Edmonton).